Pre-lamination is often referred to as the heart of a laminating system in the industry. And rightly so, because the lamination process takes place during pre-lamination to a large extent, where the foil is warmed up and then pressed or bonded to the glass using press rollers. However, the air that is still trapped is pressed out of the glass package during the course of pre-lamination. This followed by the autoclave process, during which the laminate foil is melted under heat and high pressure and finally bonded.
However, pre-lamination is not only responsible for the initial affixing of the foil to the glass, but also has a significant influence on the wastage that can occur due to adhesion problems, delamination or bubbles in the glass lamination product. Since the foils and the glass that are used (float glass as well as partially and fully tempered glass) are often high quality, companies take great care to keep the amount of wastage as low as possible during lamination. Because this also has a direct influence on the manufacturing costs of a glass lamination product and therefore also on the operating profit of the respective company, of course.
Pre-lamination essentially consists of 2 processes:
-
Heating zone
-
Pre-lamination press
1. heating zone
Glass and foil are heated up in the so-called heating zone during the lamination process. This can be carried out with a pre-heating zone (approx. 248 °F) and a main heating zone (approx. 428 °F) or several main heating zones, depending on customer requirements. Each lamination glass package (at least one glass / foil / glass sandwich) continuously passes through these heating zones at a certain speed until the foil has warmed up to 428 °F.
Basically, two thermal energy transport methods are available:
-
Convection
-
Radiation
-
A combination of convection and radiation
The combination of convection and radiation is crucial when it comes to being able to efficiently process glass lamination products with various types of glass with regard to their coatings.
Video: Construction of lamination system
2. PRE-Lamination press
The pre-lamination press is one of the most important work steps during lamination, and also plays a major parts in the success or failure of the overall process. The press consists of two rollers that lie vertically one on top of the other. The glass is rolled between these rollers at a certain speed and pressed at the same time.
The pressure that is needed is applied to the warm glass package with the heated foil via the rollers in order to achieve the initial adhesion between the foil and the glass, and press the air out of the laminated glass sandwich.
It is of fundamental importance to ensure that a closed and all-round edge seal is created. Without this, air can penetrate into the laminating glass product during the autoclave process, among other things. For details concerning this problem, please refer to our blog post "How to recognise a high quality and safe glass laminate product".
As well as the rollers, the process or the actuation of the pressing force on the rollers also play an tremendously important role – you could even go as far as to say that this is the real intelligence of pre-lamination pressing. Two different technologies are available here:
-
Hydraulic or pneumatic application of pressing force
-
Application of pressing force using spindle technology
Hydraulic or pneumatic application of pressing forcE
In hydraulic or pneumatic pressure distribution, the pressing force is applied by means of cylinders, which are actuated using either liquid or air (the most frequently used variant). However, this technology has the disadvantage that there is a relatively large tolerance range as far as the press gap and the press force are concerned, and there is always the risk of leakages in the pressure circuit, which can lead to contamination (with hydraulic pressure distribution) in the press.

The hydraulic or pneumatic press is used by the majority of suppliers because the cost is lower, but the disadvantages cannot be dismissed out of hand.
The force distribution onto the pressing rollers is not even, because each side is equipped with a cylinder. This creates numerous problems – especially when special glass shapes are to be processed. It is also extremely difficult to adjust the press for an optimum edge seal with special shapes, which also increases the amount of
glass wastage.
The different glass shapes and the uneven actuation of the left and right sides of the press and the difficulty of placing the glass package exactly in the middle of the press make it even more difficult to produce a uniform edge seal.
Application of pressing force using spindle technology
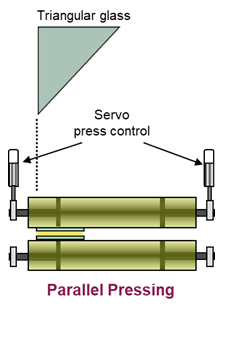
On the other hand, pressing force application using spindle technology is known to be very precise. Because the tolerance margin with this technology is very small in contrast to hydraulic and pneumatic press force application, and takes place within the range of tenths.
Furthermore, the combination of the intelligent control system and the spindle also makes it possible to carry out different pressing recipes and special shapes depending on the customer's requirements (see special shapes 1 and 2). This pressing technology can also be adjusted automatically at the push of a button within a matter of seconds - which is very complex and expensive with hydraulic and pneumatic technology.
This is why spindle technology also provides a stable process and even pressure distribution - and this also applies to special shapes. However, other complex products, such as multiple constructions for bulletproof glass or ultra-thin glass structures with 2 x 1 mm glass, can also be manufactured with the spindle without problems.
What needs to be considered when buying a pre-lamination system?
A pre-lamination system is normally purchased together with a new lamination system. However, since the pre-lamination system has to be functional in the hot area, the amount of wear is somewhat greater. As a result, the pre-lamination system may need to be replaced from time to time. Basically, this procedure is possible without problems. However, it is important to analyse exactly which products you want to manufacture now and in the future and organise the system accordingly.
To save costs, only 1 heating zone and 1 press are often installed. This may well be OK for standard PVB foils. However, if complex foils are used or complex products are manufactured, an increased amount of convection must also be used - and then the preheating zone and a second press should definitely be considered. This will make the process operate in a stable fashion, and the amount of wastage can be significantly reduced.
Conclusion:
The pre-lamination system is rightly referred to as the heart of a lamination system, since the majority of the laminating process takes place there. On the one hand, the foils are heated up and bonded to the glass. The following two technologies are used for pre-lamination: Heating zones and the pre-lamination press. In the heating zones, the foil is heated to around 60 ° Celsius in order to then be pressed to the glass in an optimum way in the pre-lamination press by means of hydraulic or pneumatic press force application or using so-called spindle technology. It is particularly important to have an optimal edge seal, which then also makes the autoclave process run smoothly.