In allen möglichen Bereichen, in denen Glas zum Einsatz kommt bzw. verbaut wird, steigen die Sicherheitsstandards ständig an – darum gewinnt das Laminieren auch in der Glasindustrie immer weiter an Bedeutung. Aufgrund der Komplexität dieses Prozesses ist es allerdings entscheidend, die dabei auftretenden Herausforderungen und Stolpersteine genau zu kennen, um entsprechend agieren, respektive reagieren zu können.
Nur so kann ein reibungsloser und stabiler Laminierprozess sichergestellt werden, der wiederum eine Voraussetzung für qualitativ einwandfreie und optimale Endprodukte ist.
Diese Fachkenntnisse gepaart mit einem exzellenten Vorverbund helfen aber auch, die Produktionskosten zu senken, da auf diese Weise die Prozessdauer und der Glasausschuss deutlich reduziert werden können. Dies gilt vor allem dann, wenn komplexe Folien oder etwa ein vorgespanntes oder teilvorgespanntes Glas verwendet werden. Etwaige Fehler, die beim Laminieren gemacht wurden, sind nach dem ersten Verpressen des Glases im Vorverbund oder nach dem Autoklaven-Prozess deutlich zu sehen.
Bei vorgespanntem Glas ist die Glasebenheit eine wichtige Voraussetzung für ein hochwertiges Glaslaminat-Produkt. Aufgrund der hohen Temperatur (über 600°C) und der eingesetzten Keramiktransportrollen kommt es bei der traditionellen Vorspanntechnologie mit Rollenöfen zur sogenannten Roller-Wave und anderen Deformationen im Glas, die den Laminierprozess erschweren können.
Daher sollte das Glas mindestens den Normen EN 12150-1 für ESG und EN 1863-1 für TVG entsprechen. Um letztendlich eine gute Qualität und einen stabilen Prozess zu erzielen ist eine noch bessere Glasqualität empfehlenswert. Je besser die Ebenheit der vorgespannten Gläser ist, umso dünnere Folien können eingesetzt werden, aber auch der Laminierprozess wird stabilisiert bzw. Delamination wird verhindert, wodurch auch die Produktions- und somit auch die Produktkosten reduziert werden können.
Nach dem Vorverbund Prozess ist auf folgende Punkte zu achten:
- Randverbund
- Presskraft
- zu kalt verpresst
- zu warm verpresst
1. Randverbund
Einen guten Randverbund erkennt man daran, dass der Randbereich des Verbundglases auf einer Breite von rund 20 mm transparent ist. Dies ist ein klarer Hinweis dafür, dass Folie und Glas optimal aneinanderhaften.
Im restlichen Laminat hingegen ist noch die Folienstruktur zu erkennen. Sie sollte über den gesamten Bereich gleichmäßig aussehen. Daran erkennt man, dass die Presskraft der Presswalzen und Erwärmung durch Konvektion- oder Strahlungsheizung während des Laminierens immer schön gleichmäßig waren.
2. Presskraft
Vor allem zwei Technologien kommen im Vorverbund zum Einsatz, um Druck mit den Pressrollen auszuüben:
- die hydraulische bzw. pneumatische Presskraftaufbringung mittels Zylinder
- die Spindeltechnologie
Die hydraulische bzw. pneumatische Presskraftaufbringung mittels Zylinder
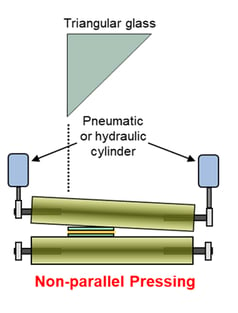
Die hydraulische bzw. pneumatische Presskraft-aufbringung mittels Zylinder ist zwar von der Bauart einfacher und somit kostengünstiger, bringt allerdings eine Vielzahl von Herausforderungen mit sich. Und wenn keine rechteckigen Glasscheiben, sondern beispielsweise Rauten oder Dreiecke verwendet werden, die insbesondere in der Architektur an Beliebtheit gewinnen, dann steigt die Komplexität mit dieser Technologie noch einmal deutlich an. Auch rasche und vom Timing her exakte Druckänderungen sind damit nur begrenzt möglich. Diese sind aber gerade bei großen Glasausschnitten im Laminat erforderlich, um einen optimalen Randverbund zu erstellen.
Zudem muss das Glasprodukt bei dieser Technologie immer in der Mitte des Vorverbunds verpresst werden, da sonst ein paralleles Pressen mittels Zylinder nicht garantiert werden kann. Die Folge können ein ungleichmäßiger Randverbund bzw. eine nicht gleichmäßige Laminatdicke sein, was den weiteren Prozessverlauf wiederum verkomplizieren und die Taktzeit reduzieren kann. Dadurch werden permanente Nachjustierungen der Presse nötig, die letzten Endes nicht nur den Glasausschuss, sondern auch die Kosten deutlich steigern können.
Die Spindeltechnoligie
Die Spindeltechnologie kommt viel seltener zum Einsatz, was vermutlich daran liegt, dass sie die kostenintensivere Technologie ist. Dennoch bringt sie einige Vorteile mit sich. Das Arbeiten mit der Spindeltechnologie ist nachhaltiger und eliminiert die oben genannten Probleme. Dies gilt vor allem bei Produktionen mit Spezialgläsern im Architekturbereich – hier kann der Pressvorgang sehr effizient durchgeführt werden, das Ergebnis: höchste Qualität und daher auch geringerer Produktkosten aufgrund geringeren Ausschusses.
Zudem lässt sich diese Technologie mittels Knopfdrucks justieren, und die Spindel ist in puncto Lebensdauer und Prozesssicherheit wesentlich stabiler. Darüber hinaus kann aufgrund der gleichmäßigen Druckverteilung auf einer Referenzseite produziert und laufend kontrolliert werden, was den gesamten Prozess deutlich vereinfacht.
Außerdem sind hier auch dann ein stabiler Prozess sowie eine hohe Produktqualität gewährleistet, wenn die Produktion nicht permanent exakt in der Mitte der Anlage vollzogen wird. Wenn eine Servo-Spindel zum Einsatz kommt, wird zudem einerseits eine sehr schnelle und exakte Presskraftanpassung und andererseits – durch den formschlüssigen Antrieb – ein paralleles Pressen ermöglicht.
Eine nicht korrekt eingestellte Presskraft führt dazu, dass die Luftblasen, die sich zwischen Glas und Folie befinden, nicht herausgepresst werden und der Randverbund unzureichend ist. Dieses Phänomen ist bereits nach dem Prozess des Vorverbunds ersichtlich und kann im Autoklav-Prozess im Extremfall sogar zur kompletten Delamination führen.
Beim hier abgebildeten Beispiel wurde zuerst mit der richtigen und dann nahezu ohne Presskraft verpresst. Nach dem Vorverbund kann sich das Glasprodukt wie folgt zeigen:
Grafik: links ohne Presskraft, rechts mit richtiger Presskraft
3. Zu kalt verpresst
Wenn vor dem Pressvorgang zu wenig Energie eingebracht, also zu kalt verpresst wird, dann verschwinden die transparenten 20 mm (Vergleiche Abb. 1 mit Abb. 2) im Randbereich des Verbundglases, die bei einem optimalen Ergebnis sichtbar sind. Und dies ist ein klares Indiz dafür, dass die Haftung zwischen Folie und Glas nicht ausreichend ist. Nach dem Autoklaven-Prozess kann dies zu einer Vielzahl von Problemen führen, wie zum Beispiel dem Phänomen des sogenannten „Blow-in“ (siehe weiter unten).
4. Zu warm verpresst
Aber auch ein zu viel an eingebrachter Energie ist nicht optimal. Dann wird das Laminat nämlich zu warm verpresst. Dadurch wird die Folie zu weich und klebrig, was man daran erkennt, dass das Glaspaket nahezu durchsichtig ist. Dabei haftet die Folie bereits vor dem Entlüften mittels Presswalze zu stark am Glas, wodurch die Restluft mitunter nicht sauber aus dem Laminat gepresst werden kann.
Im Autoklav dehnt sich diese Restluft aus bzw. wird aufgrund der fehlenden Folienhaftung am Glas sowie durch die 12 bar Überdruck noch zusätzlich Luft ins Laminat gepresst. Dadurch bilden sich viele kreisrunde Blasen und das Glaspaket erscheint nicht transparent, wie es eigentlich sein sollte:
Hier noch einmal der direkte Vergleich von zu kalt vs. zu warm:
Nach dem Autoklaven Prozess können folgende Phänomene auftreten
Nach dem Vorverbundprozess werden die Laminierglaspakete im Autoklav mit einem definierten Druck und bei hohen Temperaturen für eine bestimmte Zeit komplett verpresst.
Folgende Qualitätsprobleme können dabei entstehen:
- Blow In
- Air trapped
- Offset
- Autoklaven Kühlprobleme
- Blasenbildung aufgrund falscher Haltezeit
- Mineralische und organische Verunreinigung
1. Blow In
Vom sogenannten Blow in spricht man, wenn das Rezept im Autoklaven nicht korrekt eingestellt wurde - also, wenn beispielsweise der Druck zu schnell gesteigert - und dadurch wieder Luft in das Laminat gedrückt wird. Dies kann auch passieren, wenn der Randverbund nicht sauber verschlossen ist. Dieses Beispiel zeigt, wie wichtig es ist, einen guten Randverbund zu haben.
2. Air trapped
Air trapped bedeutet, dass nicht die ganze Luft aus einem Laminier Glaspaket gedrückt wurde. Dieses Qualitätsproblem kann durch folgende Faktoren entstehen:
- Nicht optimales Verpressen im Vorverbund
- Zu warm im Vorverbund (Folie zu klebrig)
- Roller Waves bei vorgespanntem oder teilvorgespanntem Glas
- Zu hohe Luftfeuchtigkeit
Bei einer zu starken Wärmeeinbringung im Vorverbund wird die Folie klebrig und die vorhandene Luft kann nicht ordentlich aus dem Glaspaket gedrückt werden.
Wenn Glas vorgespannt wird, können durch die hohe Temperatur und die Keramiktransportrollen wellenartige Unebenheiten im Glas entstehen. Dies kann dazu führen, dass sich das Glas schließt, bevor die Luft aus dem Glaspaket gedrückt werden kann.
Zudem entstehen durch diese Unebenheiten im vorgespannten Glas unterschiedliche Spaltweiten zwischen den beiden Gläsern in einem Laminat, die dann von der Folie aufgefüllt werden muss. Da die Laminationsfolie jedoch nur begrenzt Unebenheiten kompensieren kann, müssen in diesem Fall dickere oder mehrere Folienlagen eingesetzt werden.
Bei zu hoher Luftfeuchtigkeit ist die Folie zu „nass“. Erst bei den hohen Temperaturen im Autoklaven-Prozess kann sich die Feuchtigkeit ausdampfen, wodurch wiederum Blasen entstehen. Die Verbindung zwischen Folie und Glasoberfläche, die sogenannte Adhäsion, geht auf diese Weise verloren.
3. Delamination
Beim Delaminieren löst sich der Verbund zwischen Glas und Folie wieder auf. Dieses Phänomen tritt auf, wenn zum Beispiel die PVB-Folie, die am Seitenrand des Glases zugänglich ist, im Wasser steht oder laufend mit Wasser in Berührung kommt. Aber auch, wenn es bereits beim Laminierprozess zu Schwierigkeiten gekommen ist, kann es zur Delamination kommen. An diesem Beispiel (siehe Bild) zeigt sich erneut, wie wichtig ein guter Randverbund ist.
Darüber hinaus kann eine nicht sachgemäße Lagerung der Folie, die dadurch einen zu hohen Feuchtigkeitsanteil hat, zur Delamination führen. Dadurch reduziert sich die Adhäsion zwischen Glas und Folie, was entweder nach dem Autoklaven zu ersten Delaminationserscheinungen führen kann - ersichtlich durch runde Blasen (Eisblumen). Oder erst nach dem Einsatz des Produktes beispielsweise in einer Fassade. Aber auch die Qualität der „Verklebung“ wird so reduziert.
Bei der Lagerung und Verarbeitung der PVB-Folien ist es wichtig, die Temperatur konstant bei rund 18-22°C und die Luftfeuchtigkeit etwa bei 25-30% relative Feuchtigkeit zu halten. Dafür benötigt man einen guten Klimaraum, der in der Lage ist, diese Bedingungen zu gewährleisten.
Aber auch Materialunverträglichkeiten wie Weichmacher-wanderungen sind oft Ursache von Delaminationserscheinungen, die sich erst nach mehreren Monaten oder Jahren an den verbauten Laminaten zeigen können.
4. Offset
Das Problem des Offsets kann beim Positionieren und übereinanderlegen des Glases im Bereich des Zusammenbaus oder im Vorverbund entstehen.
Wenn im Vorverbund kein Motor für den Antrieb der Pressrollen sorgt, müssen diese einwandfrei synchronisiert sein, da es sonst durch eine ungleiche Geschwindigkeit zu einem Versatz kommt. Aber auch durch eine unregelmäßige Abnutzung der Pressrollen kann es nach einer gewissen Zeit zu Offset-Erscheinungen kommen.
Bei kleineren Laminaten bzw. dünneren Deckgläsern kann auch ein falsches Ansetzten der Pressrolle an der Laminatvorderkante Glasverschiebungen verursachen. Die Auflageflächen sollten immer exakt in einem Winkel von 90° zur Rückwandabstützung am Autoklavenrack liegen, da es sonst ebenfalls zu einem Glasversatz kommen kann - dies gilt vor allem für große und schwere Gläser.
5. Autoklav Kühlproblem
Gerade weil die Parameter Druck, Zeit und Temperatur so genau definiert sind, spielt der Autoklav eine so wichtige Rolle beim Laminieren. Sollten zum Beispiel das Kühlregister defekt oder die Kühlleitungen verkalkt sein, kann die Kühlkurve nicht eingehalten werden und die Laminierglasprodukte sind noch zu heiß, während der Druck bereits abgebaut wird. Dadurch kann es zur Blasenbildung im Kantenbereich kommen.
6. Blasenbildung durch falsche Haltezeit
Je nach Glasaufbau des Laminierprodukts muss das richtige Programm erstellt und ausgewählt werden. Eine wesentliche Rolle dabei spielt die Haltezeit, jene Zeit, in der Druck und Temperatur gleichzeitig vorhanden sind. Eine zu kurze Haltezeit führt dazu, dass die Folie nicht vollständig aufschmilzt und dadurch Freiräume im Laminat, hervorgerufen durch Glasunebenheiten, nicht schnell genug und ausreichend mit der Folie ausgefüllt werden können.
7. Mineralische und organische Verunreinigungen
Derartige Verunreinigungen entstehen meist durch die Waschmaschine und sind auf eine mangelhafte Wartung der Wasseraufbereitung zurückzuführen.
Zu den mineralischen Verunreinigungen zählen beispielsweise Kalk und Salze, zu den organischen etwa Algen. Beide können im weiteren Verlauf die Haftung (Adhäsion) negativ beeinflussen, was letztlich wieder zur Delamination führt.
Grundsätzlich kann man sagen, dass organische und mineralische Verunreinigungen vorwiegend auf die Wasseraufbereitung zurückzuführen sind. Rückstände von Schneidöl oder sonstigen Verunreinigungen an der Glasoberfläche sind zumeist auf die Qualität der Waschmaschine zurückzuführen.
Daher sollte immer darauf geachtet werden, dass die Wasseraufbereitung das Wasser mit einem maximalen Leitwert von 10 µS bereitstellt. Eine Waschmaschine, die für eine Laminieranlage geeignet ist, muss Verschleppungen von Schmutzwasser verhindern und in der Trockenzone Glasoberflächen und Glaskanten absolut tropfenfrei trocknen.
Fazit
Der Laminiervorgang gewinnt auch in der Glasindustrie weiter an Bedeutung. Dies liegt vor allem daran, dass die Sicherheitsstandards beim Verbauen von Glasbauteilen deutlich angehoben wurden und laufend verbessert werden. Um den Herstellungsprozess stabil und reibungslos zu gestalten, ist allerdings ein fundiertes Fachwissen nötig. Nur so können eine optimale Qualität der Endprodukte und die Erfüllung der sicherheitstechnischen Anforderungen gewährleistet werden.