Der Vorverbund wird in der Branche gern als das Herzstück einer Laminieranlage bezeichnet. Und das mit Recht, denn der Prozess des Laminierens findet zu einem Großteil im Vorverbund statt, wo die Folie erwärmt und dann mittels Presswalzen mit dem Glas verpresst respektive verbunden wird. Im Rahmen des Vorverbunds wird aber auch die noch eingeschlossene Luft aus dem Glaspaket gepresst. Erst danach folgt der Autoklaven-Prozess, bei dem die Folie des Laminats bei Hitze und hohem Druck aufgeschmolzen und final verklebt wird.
Der Vorverbund ist aber nicht nur für das erste Anheften der Folie am Glas verantwortlich, sondern hat auch einen wesentlichen Einfluss auf den Ausschuss der durch Haftungsprobleme, Delamination oder Blasen im Glaslaminier-Produkt entstehen kann. Da die zum Einsatz kommenden Folien und das Glas (Float Glas sowie teil- und vollvorgespanntes Glas) oft sehr hochwertig sind, achten die Betriebe sehr darauf, den Ausschuss beim Laminieren so gering wie möglich zu halten. Denn dieser hat natürlich auch einen direkten Einfluss auf die Herstellkosten eines Glaslaminier-Produktes und somit auch auf den operativen Gewinn des jeweiligen Unternehmens.
Der Vorverbund besteht im Wesentlichen aus 2 Prozessen:
-
Heizzone
-
Vorverbundpresse
1. Heizzone
Glas und Folie werden beim Laminiervorgang in der sogenannten Heizzone aufgewärmt. Je nach Kundenwunsch kann diese mit einer Vorheizzone (ca. 120° Celsius) und einer Hauptheizzone (ca. 220° Celsius) bzw. mehreren Hauptheizzonen ausgeführt werden. Jedes Laminier-Glaspaket (mindestens ein Glas/Folie/Glas-Sandwich) durchläuft diese Heizzonen kontinuierlich mit einer bestimmten Geschwindigkeit, bis sich die Folie auf 60° Celsius aufgewärmt hat.
Grundsätzlich stehen drei Methoden des Wärmeenergietransports zur Verfügung:
-
Konvektion
-
Radiation
-
Kombination aus Radiation und Konvektion
Die Kombination von Konvektion und Radiation ist entscheidend, wenn es darum geht, Glaslaminier-Produkte mit unterschiedlichen Glastypen – hinsichtlich ihrer Beschichtungen – effizient bearbeiten zu können.
Video: Aufbau Laminieranlage
2. Vorverbundpresse
Die Vorverbundpresse ist einer der wichtigsten Arbeitsschritte beim Laminieren und entscheidet sehr stark auch über Erfolg oder Misserfolg des gesamten Prozesses. Die Presse besteht aus zwei Rollen, die vertikal übereinander liegen. Das Glas wird in einer gewissen Geschwindigkeit zwischen diesen Walzen durchgerollt und dabei verpresst.
Über die Rollen wird der nötige Druck auf das warme Glaspaket mit der aufgeheizten Folie ausgeübt, um die erste Haftung zwischen Folie und Glas herzustellen und die Luft aus dem Verbundglas-Sandwich zu pressen.
Von elementarer Bedeutung dabei ist es, einen geschlossenen und umlaufenden Randverbund zu gewährleisten. Denn ohne einen solchen kann während des Autoklaven-Prozesses mitunter Luft in das Laminierglas-Produkt eindringen. Details zu diesem Problem entnehmen Sie bitte unserem Blogbeitrag „Daran erkennen Sie ein qualitativ hochwertiges und sicheres Glaslaminat-Produkt“.
Neben den Rollen, spielen aber auch der Prozess bzw. die Ansteuerung der Presskraft auf die Rollen eine enorm wichtige Rolle – man könnte sogar so weit gehen und behaupten: genau darin liegt die tatsächliche Intelligenz des Vorverbundpressens. Hier stehen zwei unterschiedliche Technologien zur Verfügung:
-
Hydraulische bzw. pneumatische Presskraftaufbringung
-
Presskraftaufbringung durch Spindeltechnologie
Hydraulische bzw. pneumatische Presskraftaufbringung
Bei der hydraulischen oder pneumatischen Druckverteilung erfolgt die Presskraftaufbringung mittels Zylinder, die entweder mit Flüssigkeit oder mit Luft (die häufigere Variante) angesteuert werden. Diese Technologie hat jedoch den Nachteil, dass es einen relativ großen Toleranzspielraum bei Pressenspalt und Presskraft gibt und zudem immer die Gefahr von Leckagen im Druckkreislauf entstehen können, die unter anderem auch zu Verunreinigungen (bei hydraulischer Druckverteilung) in der Presse führen.

Die hydraulische bzw. pneumatische Presse wird zwar aufgrund ihrer niedrigeren Kosten von den meisten Lieferanten eingesetzt, die Nachteile sind allerdings nicht von der Hand zu weisen.
Da jede Seite mit einem Zylinder ausgestattet ist, findet die Kraftverteilung auf die Presswalzen nicht gleichmäßig statt. Dadurch entsteht eine Vielzahl von Problemen – vor allem dann, wenn Glassonderformen verarbeitet werden sollen. Auch die Einstellung der Presse für einen optimalen Randverbund gestaltet sich bei Sonderformen mitunter äußerst schwierig, wodurch der Glasausschuss ebenfalls erhöht wird.
Aber auch die unterschiedlichen Glas-formen sowie die ungleichmäßige Ansteuerung der linken und rechten Seite der Presse bzw. die Schwierigkeit, das Glas-paket genau in der Mitte der Presse zu platzieren, erschweren hierbei die Herstellung eines gleich-mäßigen Randverbunds zusätzlich.
Presskraftaufbringung durch Spindeltechnologie
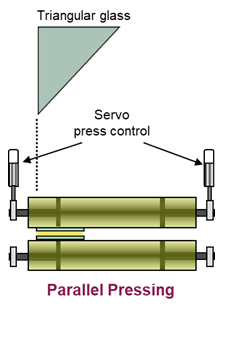
Die Presskraftaufbringung mittels Spindeltechnologie ist hingegen als sehr präzise bekannt. Denn bei dieser Technologie ist der Spielraum der Toleranz im Gegensatz zur hydraulischen und pneumatischen Presskraftaufbringung sehr gering und spielt sich im Zehntelbereich ab.
Zudem ermöglicht die intelligente Steuerung in Kombination mit der Spindel je nach Kundenwunsch auch die Durchführung unterschiedlicher Pressrezepte und Sonderformen. Diese Presstechnologie kann darüber hinaus auf Knopfdruck automatisch und sekundenschnell justiert werden - bei der hydraulischen und pneumatischen Technologie ist diese sehr komplex und aufwendig.
Deshalb erlaubt diese Spindeltechnologie auch einen stabilen Prozess und eine gleichmäßige Druckverteilung - und das gilt auch für Sonderformen. Aber auch andere komplexe Produkte wie etwa Mehrfachaufbauten für schusssicheres Glas oder ultra-dünne Glasaufbauten mit 2 x 1 mm Glas können mit der Spindel problemlos hergestellt werden.
Was muss man beim Kauf eines Vorverbundes beachten?
Im Normalfall wird ein Vorverbund mit einer neuen Laminieranlage gekauft. Da jedoch der Vorverbund im Hitzebereich funktionstüchtig sein muss, ist der Verschleiß um einiges höher. Daher kann es natürlich vorkommen, dass der Vorverbund zwischendurch ausgetauscht werden muss. Grundsätzlich ist dieser Vorgang ohne Probleme möglich. Wichtig ist allerdings, dass man genau analysiert, welche Produkte man aktuell und in Zukunft fertigen möchte und die Anlage entsprechend ausrichtet.
Um Kosten zu sparen wird oft nur eine Heizzone sowie eine Presse installiert. Für Standard-PVB-Folien mag das durchaus sinnvoll sein. Wenn jedoch komplexe Folien verwendet oder komplexe Produkte hergestellt werden, dann muss auch eine erhöhte Konvektion verwendet werden - und dann sollte unbedingt die Vorheizzone sowie eine zweite Presse in Betracht gezogen werden. Dadurch läuft der Prozess stabil und der Ausschuss kann deutlich reduziert werden.
Fazit
Der Vorverbund wird mit Recht als das Herzstück einer Laminieranlage bezeichnet, da der Prozess des Laminierens größtenteils dort stattfindet. Dabei werden einerseits die Folien aufgeheizt und mit dem Glas verklebt, aber auch ein Großteil der Luft aus dem Laminat gepresst.
Für den Vorverbund werden folgende zwei Prozessschritte eingesetzt: Heizzonen und die Vorverbundpresse. In den Heizzonen wird die Folie auf rund 60° Celsius erwärmt, um dann optimal in der Vorverbundpresse mittels hydraulischer bzw. pneumatischer Presskraftaufbringung oder durch die sogenannte Spindeltechnologie mit dem Glas verpresst zu werden. Dabei kommt es vor allem auf einen optimalen Randverbund an, der dann auch einen reibungslosen Autoklaven-Prozess ermöglicht.